Tenant Design Guidelines
Tenant Design Guidelines
- Introduction
- Purpose of Document
-
The following Design Guidelines for Tenant improvements have been established to encourage exciting concession concepts and design identity within the commercial/retail areas of the terminals at Minneapolis-Saint Paul International Airport (MSP), including Terminal 1 and Terminal 2. They are intended to ensure an orderly and aesthetically coordinated approach to storefront and sign design in keeping with the design objectives of MSP and to ensure that standards for storefronts, interior finishes and signage requirements are understood by Tenants, their contractors and their designers.
The latest edition of these Tenant Design Guidelines, together with all Lease and lease drawing documentation required by the Landlord comprise the Tenant Package. Tenants are strongly encouraged to become familiar with the intent and details of these documents prior to the commencement of their design and construction, and to become aware of the special characteristics of the terminal buildings and how their architectural elements, finishes, and materials will affect individual concession design solutions. Tenants must comply with the requirements and conditions set forth in the Tenant Package. Should there be any discrepancies between the Tenant Design Guidelines and the Lease, the latter shall govern.
The Landlord or Landlord’s Representative shall have absolute right of review and approval over all aspects of concession tenant improvements, as well as the discretion to waive any of the design guidelines so long as the concept, quality and character of the project are not significantly affected.
-
- How to Use this Document
-
Each Tenant must be familiar with the intent, scope and detailed requirements of this handbook before the design process begins. It is the Tenant’s responsibility to visit the site and verify existing conditions, including HVAC, plumbing, electrical and construction sustainability requirements. Each Tenant’s design must be approved by the Landlord before any permits are issued and construction is allowed to begin. Submittal and approval procedures are outlined in the CPIT Procedure Manual.
-
- Design Intent
Retail and food and beverage presentation within MSP will require careful consideration to scale, exposure to patrons of all abilities, visibility and circulation patterns. Design merchandising solutions should encourage store identity and product recognition through the emphasis of storefront transparency, creative concession identity graphics, vibrant merchandise display and strong overall retail identity. The application of glass and facade detailing of storefronts must reflect a standard of high environmental quality. Facades and accompanying displays should suggest the independent character of individual retailers and the quality of services and types of merchandise and food that they provide.
- Definitions
-
The following definitions are used throughout the Tenant Design Guidelines and shall be interpreted as follows:
- ADA refers to the Americans with Disabilities Act.
- Common Area is the space used by the general public that is designed and maintained by the Landlord.
- Concourses are the public circulation zones that lead from Terminal 1- to all airline gates. Currently, there are seven concourses referred to as A, B, C, D, E, F and G.
- Demising Walls are common walls that mark the lease lines between independent Concession Tenant-leased areas or other separately designed spaces, including public spaces, service corridors, gatehold, etc.
- Landlord is the Metropolitan Airports Commission (MAC) and any of its representatives.
- Lease lines (except where noted on plan exhibits) extend from the outermost point of the storefront’s exterior face into the rear of the Concession Tenant’s leased premises and from the centerline of the side demising walls.
- LEED is Leadership in Energy and Environmental Design that provides a framework for healthy, efficient, and cost-saving green buildings.
- Storefronts shall be defined as the architectural facades of any Tenant-leased premise perimeter adjacent to public circulation areas of the terminals, including doorways. The storefront will be physically defined by base building elements provided by the Landlord which surround and frame the concession tenant storefront. Elements include side piers, the upper fascia/bulkhead, and the floor surface at the lease line.
- Construction Sustainability are the requirements related to the construction of the unit.
- Tenant is the lessee, including all food and retail concessionaires in the Airport.
- Terminal 1 is the central airport building and the hub of all concourses.
- Terminal 2 is a separate building containing Gates H1-14, located approximately one mile southwest of the Terminal 1
- “Universal Design is the design and composition of an environment so that it can be accessed, understood and used to the greatest extent possible by all people regardless of their age, size, ability or disability.” https://universaldesign.ie/
-
- Landlord Work/Tenant Work
-
The following is an overview of responsibilities assumed by the Landlord for design, construction, and improvements to the concession tenant leased premises. Specific Tenant work is described, as it applies to the leased premises, in the various sections of the Tenant Design Guidelines. The Landlord will be responsible for the construction of common areas, concession tenant-leased premise shell, and all pedestrian circulation areas/systems (unless otherwise noted). In some cases, airlines tenants will be responsible as agents of MAC, and concession tenants will work both with the Landlord (MAC) and the applicable tenant airlines. The Tenant’s design construction materials will be at the sole discretion of the Landlord, and will be subject to change in accordance with the Landlord’s determination.
-
-
Pest Control
-
See MAC Design and Construction Standards Guide Specification section 10 81 00 for pest control and rodent proofing requirements.
-
-
Submission Requirements
-
See current version of CPIT Procedure Manual for submission details.
-
- Purpose of Document
-
Accessibility
-
Minimum Code Requirements: All projects constructed at MSP must, at a minimum, meet the requirements of the ADA and MN Chapter 1341.
-
Universal Design: MAC expects concessions concepts to consider and incorporate the definition and seven principals of Universal Design (Equitable Use, Flexibility in Use, Simple and Intuitive Use, Perceptible Information, Tolerance for Error, Low Physical Effort, Size and Space for Approach and Use). The following guidelines contribute to achieving this goal:
-
Vertical Merchandising is recommended for both its ability to increase sales and more universal accessibility to products offered.
-
Accessible seating shall be provided and distributed as described: 10 percent of total, but not less than two of each type of seating provided shall be accessible. This shall include bar, tables, and community tables.
-
Clear space: Aisle widths must be adequate for passengers with baggage or luggage carts and also accommodate people with disabilities, particularly those who use wheelchairs.
-
-
-
Storefront
- Storefront construction shall extend from the floor slab to the horizontal neutral bulkhead or ceiling above and shall abut the vertical demising systems at both sides of the demised concession tenant’s premises. Upon request, Landlord will consider design elements that extend beyond tenant lease line.
- Neutral piers and fascia will be built by the Tenant, with Landlord-selected finishes abutting the lease line to be selected by the Landlord’s architect. If an existing Tenant space is re-demised, it shall be the Tenant’s responsibility to construct a new neutral pier.
- Any soffit or neutral pier returns exposed by recessing the storefront shall be finished to match the Landlord’s neutral surround construction and finishes by the Tenant at Tenant’s cost.
- The Tenant may not attach to or support their storefront from any part of the concourse neutral fascia (except for lateral support only).
- No element of the storefront may extend beyond the concession tenant’s lease line with the exception of specified storefront blade signs where permitted by the specific criteria. The CPIT process does allow for the Tenant to propose elements that extend beyond the lease line for consideration.
- All storefronts, except entry doors, shall have a minimum 6” high base of durable and maintainable material integrated with the storefront design. Acceptable materials include brass, chrome, aluminum, natural stone, or hardwood.
- High transparency in the storefront design is encouraged. The Concession Tenant’s overall storefront area shall have a minimum of 75% visual transparency/openness unless otherwise specified in the subsections included under the location-specific Design Guidelines.
- Storefront Entries
- A limited portion of the Tenants’ overall storefront area shall be designated as storefront entries.
- Storefronts shall have total opening width at least 1/3 of the total storefront leased-area width.
- If the Tenant’s storefront faces onto two common area concourses, tenant storefronts may have as many as two open entryways.
- Openings or setbacks from the storefront lease line will be prohibited within 5’-0” of any demising pier unless otherwise specified within specific Design Guidelines.
- No part of any door swing shall extend beyond the storefront, lease line, construction barrier or into the airport’s public corridors.
- Any flooring between the lease line and the Tenant storefront or closure line is the responsibility of the Tenant and must either match the common area flooring or match the Tenant floor finish. Common area flooring finishes vary depending on the location in the airport and may be terrazzo, carpet, or tile.
- Electronic surveillance or other shoplifting detection devices and security systems shall be the responsibility of the tenant and integrated within Tenant’s storefront design, freestanding posts or columns. Suspended boxes, suspended rails or other exposed equipment or decals are not permitted.
- The soffit at the recessed entries shall be a minimum of 8’-6” above the finished floor, unless otherwise specified elsewhere in the Tenant Design Guidelines.
- Recessed down lights are required for the recessed entry area. Illumination of these lights must be controlled by a time clock.
- Storefront Closures
- The Tenant shall provide a new storefront closure system. The following systems are permitted. In the Main Mall, the MAC’s preference is for a glass system.
- Recessed, hinged outswinging doors with multipane glass, fully glazed, or frameless glass doors on pivots. Doors must not swing beyond the lease line when fully opened.
- Sliding glass doors which slide behind one another and stay open; these doors must be pocketed in and above the storefront enclosure unless specifically approved by the Landlord.
- Side folding or overhead coiling grilles are acceptable as long as all portions of the frame or track that are visible match the metal finishes used elsewhere in the storefront. Grilles must be independently supported. The Landlord’s structure may be used for lateral support only. The structural support for the rolling grille must be incorporated into the Tenant’s storefront design.
- If side folding grilles are installed, provide access for cleaning pockets.
- The Tenant shall provide a new storefront closure system. The following systems are permitted. In the Main Mall, the MAC’s preference is for a glass system.
- Display Areas
- Display area is defined as the first 5’ of the Tenant area beyond the lease line.
- The use of creative display areas is strongly encouraged. Innovative merchandising, quality materials and appropriate lighting should be used to convey the Tenant’s merchandise identity and generate activity and excitement.
- Digital displays are allowed provided they have no sound, do not project advertisements nor broadcasts, and all content is approved by the Landlord.
- Floor finishes shall be limited to durable materials such as stone, ceramic tile, and wood. Carpet and vinyl flooring are prohibited in this area.
- All show windows shall be adequately lighted and ventilated. This area shall be illuminated with low voltage track lights, recessed lighting, or approved specialty lighting.
- Lighting in this area shall be on a dimmer. Glare visible to the common area will not be permitted.
- No linear tube fluorescent lighting or acoustical tile ceiling will be permitted in display areas.
- Tenants are encouraged to provide ceiling heights as high as possible within the display area.
- All fixtures shall be professional and industry standard for display windows. No pegboard or metal shelving of any kind is permitted.
- No signs shall be taped or fastened to the display windows or hung from the soffit.
- No checkout counters, temporary sale racks or mass merchandising systems (slatwall) are allowed in the display area.
- Storefront Finish Materials
- All storefronts shall be constructed of the highest quality, durable materials that can easily be maintained. Tenants are encouraged to use materials in a creative manner. All materials and their finished installation are subject to the approval of the Landlord. Storefront material must comply with the building code for flame spread and smoke development ratings and construction sustainability requirements.
- Acceptable Materials:
- Marble, granite, limestone and other natural stone products
- Wood-top grade mill quality, natural or stained finish hardwood
- Ceramic tile
- Decorative finished metals such as polished chrome, stainless steel, brass, bronze, anodized aluminum or factory painted steel may not comprise more than 10% of the storefront.
- Frameless clear glazing of tempered or laminated safety glass with polished exposed edges
- Framed clear glazing with wood or metal glazing mullions, only if acceptable to Landlord based on Tenants design intent
- Ornamental glass, such as tinted, etched, sandblasted, stained, beveled, or leaded
- All glass used in a store front must be safety glazing
- Any other materials approved by the Landlord
- Restricted Use Materials:
- Special coatings such as Zolotone and Polymyx may be allowed at the Landlord’s discretion. These special coatings will only be considered when used in limited areas, as accents, when applied to sound, smooth durable substrates and in areas inaccessible to the public.
- Unacceptable Materials:
- Simulated materials of brick, stone or wood, except as noted in restricted materials
- Painted gypsum board
- Wallpaper or wallcovering
- Rustic materials such as rough wood, “distressed” wood, diagonal wood siding, or used brick
- Plywood paneling
- Hardboard or high-density particle board
- Pegboard in any form
- Mill finish aluminum or field painted metal
- Cork or cork tile
- Carpet or fabric
- Plastic laminates
- Plexiglas, fiberglass sheeting, or mirror
- Other materials which, in the sole opinion of the Landlord, are of poor quality, inappropriate finish, or incompatible with adjacent Tenant or mall finish material.
- Materials that do not meet the construction sustainability guidelines
- Single Story Common Spaces
Single-Story Common Space Storefront
- Multi-Story Common Spaces
Multi-Story Common Space Tenant Storefront
- Interior Finishes
- Demising Partitions
- Demising walls between Tenants shall be centered on the lease line dividing tenant spaces and extend to the structure above. Tenant is to use metal studs for these partitions. Each tenant space shall be separated from other tenant spaces by a one hour rated fire partition. The fire partition is not required to extend beyond the underside of the ceiling.
- Demising walls along exit corridors and other Landlord spaces will be provided by the Landlord from floor to structure above, with accommodation of existing HVAC, plumbing, electrical, etc. When constructed of metal studs, the Landlord will provide gypsum board on the Landlord side only. The Tenant shall provide finishes on their side of the lease line wall.
- The Tenant must fire stop around all structural shapes, ducts, pipes and other penetrations through the fire partition or demising walls. The space above the finished ceiling is used as an air plenum. Therefore, if the Tenant’s wall is constructed solid to the structural deck above, provisions must be made for return air to the Landlord’s HVAC unit.
- Additional wall reinforcement or independent support is required for demising walls used to support shelf standards or other heavy attachments.
- The Tenant shall furnish and install a minimum 3’-0” wide by 7’-0” high door connecting to the service corridor. Doors to exit corridors must be fully recessed so as not to project into the corridor when open. The door recesses, where required, shall be provided by the Tenant. All doors and frames opening into the Landlord’s corridor shall conform to the MAC Design and Construction Standards specifications. All doors, frames, and recesses shall be painted to match the corridor paint color. All interior doors used to access fire exit corridors shall be labeled fire door assemblies, complying with local codes and MAC Standards.
- Wall Finishes
- All wall surfaces in the sales area visible to the public must be finished in an acceptable manner. The wall treatments should reflect the image established at the storefront. Finishes considered to be suitable are painted gypsum board or plaster, commercial grade wall coverings, wood moldings or panel treatments, decorative metal, or natural stone.
- Walls in food preparation and utensil washing areas must be smooth, durable, non-absorbent, and easily cleanable.
- The use of the following materials will not be allowed as a wall material in areas visible to the public:
- Extensive use of mirrors or common slatwall,
- Simulated brick or stone,
- Wood grained or simulated pattern plastic laminates,
- Pegboard or corkboard,
- Plywood and rustic or rough sawn wood,
- Carpeting on walls,
- Any other material as determined by the Landlord.
- Any material that does not meet the construction sustainability requirements
- Wall treatments should be finished at the floor with a durable base material such as wood, stone, ceramic tile, or stainless steel. Vinyl or rubber base will not be permitted in areas visible to the public.
- Surface mounted shelf standards will not be accepted.
- Floor Finishes
- A suitable floor finish must be provided by the Tenant at all public areas of the Tenant’s premises. The elevation of the finish floor must match the adjacent common area floor. Bull-nosed tile, reducer strips, or carpet edge guards will not be permitted.
- Floor treatments should be designed to reinforce the character of the store concept and image.
- A hard surface floor material is required at the storefront lease line and must extend at least five feet into the store. Acceptable hard surface treatments include natural stone, hardwood strip floors, or terrazzo. Refer to Specific Design Criteria for exceptions.
- Floor finish materials that are not permitted in sales areas or areas visible by the public are quarry tile, rubber/vinyl flooring, vinyl composition tile, or wood parquet flooring.
- When carpeting is used, the Tenant is encouraged to use patterns and borders to define areas of the store. Carpeting must be of superior quality. Direct glue-down installation is recommended or as approved by Landlord. It is important that flush transitions to other materials be provided to minimize visual distractions and walking hazards. Reducer strips of any kind are not acceptable.
- Tenants must install a sheet anti-fracture waterproof membrane under all tile floor installations, including floor slab and floor penetrations in all toilet rooms, kitchens and similar water-prone areas. Rolled on liquid or fluid membranes are not allowed. The waterproofing must extend a minimum of 4” up the perimeter walls of such areas. Tenant must provide material or devices required to prevent the passage of water or liquids out of these areas.
- The Tenant is required to repair the interior slab as required to provide a smooth, sound substrate to receive tenant finishes.
- If an expansion joint occurs within the tenant space, it shall be the Tenant’s responsibility to install the finish floor material to this joint in a workmanlike manner. The Landlord will not be responsible for finished floor material installed over expansion joints.
- Ceiling Finishes
- The Tenant is required to provide a ceiling throughout the premises. Exposed structure is not permitted. Provide expansion joints consistent with industry standards. Location of all access panels for above ceiling shut off valves, plumbing traps, electrical controls, etc. shall be shown on the ceiling plan at the time of CPIT plan submittal.
- Approved ceiling systems for the sales area or any area visible to the public include the following:
- Painted gypsum board or plaster,
- Concealed spline acoustical tile,
- 2’ x 2’ acoustical tile with tegular edge.
- Access must be provided by the Tenant to any Landlord’s equipment, valves, controls, piping, etc., located above the Tenant’s ceiling.
- Ceiling suspension systems may not be fastened to the underside of the metal roof deck, piping or ductwork above. All fastening devices must be secured to the structure above.
- Combustible materials of any type are not permitted above the finished ceiling.
- Ceilings not terminated tight against a wall surface must be returned to the deck above and sealed.
- Ceilings in food preparation and utensil washing areas must be smooth, durable, non-absorbent, and easily cleanable.
- Store Layout
- Tenants shall give careful consideration to the use of colors and materials on all floor, wall, and ceiling surfaces, complementing the aesthetic and quality established in the main public areas.
- Layouts should react to passengers’ limited time with displays arranged to encourage impulse purchase, ease of browsing and speed of transaction.
- Displays should be attractive and call attention to the products featured, but must not interfere with the egress or access to the store.
- Aisle widths must be adequate for passengers with baggage or luggage carts and also accommodate people with disabilities, particularly those who use wheelchairs.
- Restaurants, lounges, and snack bars should have room available near or underneath tables for the storage of bags and packages.
- The Tenant shall designate a drop site inside the unit for deliveries.
- Lighting Guidelines
-
The interior lighting system shall comply with the State of Minnesota Energy Code and construction sustainability requirements. These Criteria shall govern the design and installation of all store lighting by Tenant that is visible from the public areas of the terminals. Tenants shall install all lighting subject to the following requirements:
-
Window display lighting shall be LED. In general, light sources (including lamps) shall not be visible from the terminal public corridors.
-
Spotlights may be recessed, adjustable angle fixtures, or track-mounted adjustable spotlights. All adjustable units must be focused so that brightness is not visible from public area walkways, with the exception of small halogen spotlights.
-
Interior General Lighting
- General lighting fixtures for the store interior shall be of the glare-free type.
- LED source light fixtures are required for all areas of the tenant space for energy conservation and longevity of the source. LED fixtures shall have a diffusing lens or panel, such that individual diodes are not visible to the public. Fixtures shall be glare free or glare controlled.
- Incandescent lighting is prohibited as a light source.
- Bare lamp fixtures are not acceptable.
- Acceptable color temperatures of lamps is 3000K or 3500K with a Color Rendering Index (CRI) of 80 or higher.
- Surface or pendant-mounted track and track fixtures installed for accent lighting may be used.
- The track and fixtures shall be painted to match the ceiling color of Tenant’s store. If the track and track fixtures are a part of the interior decor and other paint finishes are required, they must be approved in advance (in writing) by the Landlord.
- Decorative type lighting, such as pendant units, chandeliers, or wall brackets, may be used only if Tenant has established an identity based on this design theme, and must be approved in advance of build-out by Landlord. No strobe, spinner or chase-type lighting shall be used.
- Luminous ceilings must be approved by the landlord.
- No lighting shall be installed in the common area ceiling for any purpose.
- All self-illuminated showcases and display cases must be adequately lit and ventilated. Direct visual exposure of the light source is prohibited.
- A seven-day, calendar type, 24-hour timing device shall be provided by the Tenant for lighting of Tenant’s storefront and show window areas during required hours which will be designated by the Landlord.
- Interior emergency lighting shall be installed as required by applicable codes.
- All lighting installations must be approved by the Landlord.
- See the “Hennepin County Construction Guide” for additional lighting requirements in food service and retail concessions.
- See Construction Sustainability Requirements for additional lighting and energy requirements in food service and retail concessions.
-
-
- Demising Partitions
- Food Court/Food & Beverage Concessions
- General Guidelines
- The Tenant shall provide a dropped bulkhead across the entire width of the storefront at the lease line, to separate the Concourse ceiling from the Tenant provided ceiling, and to create a Tenant sign band. The bottom of the bulkhead shall be 7’-4” above finished floor, and shall extend to the structure above. This sign band may project up to 1’-0” beyond the lease line if sightlines to directional signage, or to surrounding tenants, are not obstructed.
- The overhead soffit may be used to house the overhead coiling grille.
- A maximum of 100% of the storefront may be open (without glazing).
- The Tenant must provide a full-height wall separating the sales area from the kitchen, service, and storage area for security; and to shield views into the service area.
- Wall openings between the sales area and service area must be kept to a minimum. Pass-through openings shall be designed to block views into the service area.
- The finish on all walls in the sales area behind the counter shall be ceramic tile. Painted gypsum board or vinyl wall covering is not allowed.
- Ceilings shall comply with Section 3.4 and meet all Health Code requirements.
- The flooring material between the lease line and the recessed counter shall be hard surface. Slip-resistant ceramic tile, natural stone, and hardwood strip flooring are acceptable.
- Store Interior Design
- Floors shall be waterproof. All floor penetrations sealed and waterproofed using Nobel Seal TS manufactured by Nobel Company. Installation shall be in accordance with the manufacturer’s recommendations. All floor penetrations must be placed at locations approved by the Landlord’s representative and sealed. Substitutions will be considered to meet sustainability requirements.
- The Tenant shall provide a floor finish to meet local health department requirements in all food preparation areas. If required, floor leveling fill and any other preparations for the finish material installation will be provided by the Tenant.
- Acceptable Tenant floor finishes in areas visible to the public are slip-resistant ceramic tile, stone tile, and terrazzo.
- The Tenant will provide 5/8” Type “X” gypsum board at the interior of all demising walls from the floor to the underside of the ceiling to provide a one-hour fire rated assembly. Any wall penetrations below the ceiling line for mechanical ducting, piping, electrical, etc. shall be fire dampered/ fire caulked to maintain the fire rating. Tenant wall finishes shall meet local Health Department requirements in all food preparation areas.
- All roof penetrations required for the Tenant’s mechanical equipment must be coordinated with the Landlord and flashed into the existing roofing using a Landlord approved roofing contractor. Slab knockouts exist for consolidation of penetrations.
- Ceiling lighting provided by the Tenant shall be shielded or enclosed to prevent breakage. Tempered or shatterproof-coated bulbs are also acceptable. Illumination levels shall meet requirements outlined by the health department. Light fixture selections are subject to approval by the Landlord.
- Equipment, storage stock, etc. loading not to exceed 100 lbs/sf.
- Sales Counter
- The main serving counter will be constructed by the Tenant a minimum of 6’-0” behind the lease line to allow for queuing and service to occur within the Tenant space.
- The counter dimensions must comply with MN Chapter 1341 and ADA requirements.
- The front counter must present a clean, uncluttered appearance. Food service equipment, beverage dispensers, cash registers, and other equipment must be concealed from view as much as possible.
- Open storage of paper goods, packaging, and supplies is not permitted.
- Access through the front counter is not permitted, unless no rear service door is possible.
- Napkins, condiments, utensils, straws, and trays must be concealed behind the front counter or recessed into the countertop.
- Sneeze guards and/or tray slides (when required) must be custom designed as an integral part of the front counter and be constructed of glass and stainless steel or brass.
- The countertop must be constructed of solid polymer surfacing (Corian or equivalent), Granite, or manufactured Quartz. Plastic laminate or ceramic tile is unacceptable and meet the construction sustainability requirements.
- The face of the counter may be of the following materials:
- Marble or granite,
- Ceramic tile,
- Solid polymer (Corian or equivalent),
- Hardwood, stained or painted,
- Metal (stainless steel or brass),
- Other durable, non-porous material approved by the Landlord and meets the construction sustainability requirements.
- The Tenant must provide a 6” high ceramic tile base along the entire length of the counter. The base shall be recessed to create a toe space. The base must grouted solid throughout the depth of the casework.
- Glass display cases constructed of clear glass and stainless steel, brass, or bronze; will be permitted to a maximum height of 4’-8” and maximum width of 25% of the storefront width. Display cases may not extend past the face of the countertop.
- No food preparation areas or display cases are allowed in a zone 24” from the edge of each neutral pier and within 18” of the finished floor.
- Signage
- Storefront signage complying with Section 4.1, 4.2, and 4.3 may occur on the sign band provided by the Tenant.
- The maximum height of the sign letters shall not exceed 12” and the maximum height of any individual letter shall not exceed 14”.
- The maximum length of the sign shall not exceed 70% of the total storefront width. Plastic signage shall be located at least 18” from adjacent tenants and shall not be more than 20% of the wall facing the mall or concourse. Plastics used in signage shall meet the flame spread and smoke development requirements spelled out in the building code.
- In addition, each Tenant is allowed one (1) Blade Sign. Refer to Sections 6.5.1 and 6.6.1.
- Menu Board
- All Concourse Food Service Tenants are required to provide one menu board, mounted on the rear wall of the sales area or on a suspended fascia. Digital menu boards are encouraged. Menu boards are not permitted at the front lease line.
- Internally illuminated box signs must be recessed. These menu boards shall be integrated into the overall design. Provisions should be made for changing prices or products in an undetectable manner.
- Adjustable track lighting concealed from view in an alcove directly in front of the menu board is also an acceptable means of illumination for the menu board.
- All menu boards and photos of menu items shall be professionally designed and fabricated, and be integrated with the Tenant’s graphics and merchandising design.
- The menu board signage shall be of proper size, color, and illumination level to be readily visible from the common area. The storefront fascia shall not block views to the menu board.
- Product Display
- Creative display of food and beverages is required of all Tenants. Menu selections may be presented behind glass sneeze guards on the front counter.
- All pre-packaged foods must have proper nutritional labeling and expiration dates.
- Decorative products, ingredients or products in decorative packaging may be displayed on open shelves at the front counter and throughout the Design Control Area.
- Any food preparation that can be done in an attractive or theatrical fashion may be done at the front counter or in public view.
- Graphics
- Tenants are encouraged to dress up their space with professional quality graphics, photographs, and art work. Exciting and vibrant combinations and uses of materials are desirable. Any artwork displayed in a food preparation or bar area must be cleanable.
- Graphic elements must be located at a minimum of 6’-0” behind the lease line and between 5’-0” and 9’-0” above finished floor. They must be planned and designed as an integral part of the design control area.
- Disorganized or handwritten temporary signs will not be permitted. “Employment Opportunities/Help Wanted” or any signs implying such are prohibited unless approved in writing by the Landlord. “Daily Specials” advertising signs or for seasonal or temporary promotions must be integrated into the menu boards or into permanent sign holders.
- Food Court Public Seating Areas
- Food courts are essential spaces supporting multiple-concept, and sometimes multiple-tenant, quick-serve, grab-and-go, and other types of food and beverage establishments located about a central public gathering and seating area. To effectively implement sustainable, durable, cleanable, and efficiently organized public amenities such as this, the following items are provided to guide design and construction decisions for these public spaces.
- Qualities of these spaces are: well-lit, open, inviting, clearly defined and orderly seating areas that are easily navigated by passengers with companions and luggage. The introduction of daylight and views of the airport and airfield should be used when possible.
- Multi-story spaces and spaces with additional existing architectural features, such as skylights, views to airport activities, windows to airfield activities, etc., should fully utilize those existing conditions and structure public spaces leveraging those existing conditions in an architecturally harmonious method when possible.
- Finish materials utilized within the food courts shall be durable, as per existing standards and existing built-conditions and must demonstrate a reasonable opportunity for cleanliness (including perception of cleanliness), maintenance, repairs, and organization. This includes furnishings, built-in/millwork, flooring, ceilings, fixtures, light fixtures, etc.
- Seating
- Seating quantities shall be maximized, with the final ratio of seating SF to operations determined by the Concessions’ Planning and Implementation Team (CPIT), with the highest percentage of seating dedicated to solo-seating. The seating should include flexible two-tops (and some four-tops) with banquette seating. A free-floating (planned) mix of two-tops and four-tops should represent the smallest amount of seating types. Tables and counters in these areas should be 30” above finished floor. Multiple four-tops, 30” above finished floor, with legs at its corners, shall be provided at banquette seating and in open/free-floating seating areas to provide for greater accessibility. Standing-height counters (42”) may be provided in areas of limited space availability but must be coupled with equal numbers of lower counters that are at an accessible height.
- Seating shall be organized by architectural elements meant to divide food court circulation from seating, concourse circulation from seating, solo-seating from banquette seating, etc., and shall provide for an easily-reorganized seating arrangement (allowing cleaners to focus on cleaning, rather than continually straightening the area). Banquette seating shall have easily removable seats and backs for reupholstering and cleaning in open cavities. The banquette seating cavities under seating and/or fixtures shall be on 6" legs, castors or filled with a light-weight concrete slurry to for ease of cleaning and to prevent harborage.
- A minimum seating-to-prep/BOH square-foot ratio of 1:1 or greater is required for food courts and sit-down restaurants in order to provide for adequate opportunities to eat at or near the chosen venue.
- Ingress/egress from the space shall be clear and wide enough for queuing, seating, and walk-aisle paths. Well defined travel paths to the multiple units, as well as multiple entries and egress points, shall be provided coupled with disposal receptacles at exit locations. These entries shall be clearly marked and allow for views through the space to all tenant units, and may include other directional wayfinding to assist the guests with the less-visible units. Queuing shall be directly in front of unit with a clear order and pickup area for quick-serve units.
- Three (3) types of disposal receptacles shall be provided by Landlord, (1) trash, (2) recycling, and (3) organics recycling. These separate containers shall be built into architectural dividers or positioned along the dividers. In order to maximize receptacle use, the receptacles shall be placed alongside the egress paths at the exterior of the food court. A built-in fluid disposal unit adjacent to the trash receptacle will be provided by Landlord.
- Power shall be provided at counters, behind banquette hard walls, and at as many tables as possible.
- Lighting may be utilized to call out certain types of seating, create a more human-scale space, and augment general illumination. Lighting must be LED lamped, and should follow existing installed lighting types in public seating areas including food courts.
- Signage at food court tenant units shall follow existing guidelines and MAC Design and Construction Standards, overhead ‘Food Court’ signage shall be replaced, or shall remain in place to designate a common-use area.
- General Guidelines
- Concessions Signage
- General Guidelines
-
Landlord encourages signage that balances blending with the surrounding design environment, while contrasting with adjacent tenant’s signs to provide differentiation of identity. Tenants are required to design, fabricate, install and maintain storefront signs that exhibit imagination, high fabrication quality, and compatibility with adjacent and facing storefronts. Signage shall be limited to trading name and logo only, as approved by the Lease. No corporate brand names, product names, or phrases may be used on storefront signs or in any area visible to public areas without written Landlord approval. All signs must be Underwriter Laboratory (UL)-approved. No exposed raceways, ballast, transformers, sign company names or labels are permitted.
Creative signage that departs from the traditional will be required. Tenants should strive to develop signage that is an inherent part of the store concept. As the Landlord wishes for signs to be creatively integrated with base building architectural elements to form a successful composition, a specific vertical sign band has not been provided. Please reference the diagrams in this document.
The primary sign options include the following:
-
Rear-Lit Channel: Rear-lit, or halo-reverse-lit channel individually mounted metal letters illuminated with neon with the rear face of each letter no more than 2” away from the background plane of the fascia sign band. Illuminated channel letters with acrylic sides are not permitted.
-
Rear-Lit Stencil: Rear-lit, acrylic-faced characters fabricated flush to face of sign band surface.
-
Individually-Cut/Low Relief: Signs and/or letters carved and applied to sign band surface illuminated externally.
-
Formed Letter Tubing: Protected LED tubes, imitating neon, forming letters and/or Tenant logo are permitted. Dimmers are required.
-
-
Tenants may suggest other types of signs for consideration, but the Landlord must give approval prior to final design and fabrication.
-
-
Sign Types, Areas, and Sizes
-
Storefront signs should reflect the following:
-
Signs should incorporate graphic symbolism of shop name or merchandise rather than written advertising.
-
Signage should be an art form.
-
Variety and individuality will be emphasized.
-
No sign advertisement, notice, or lettering other than store names or approved logos shall be exhibited, inscribed, painted, or affixed on any portion of any storefront or have major visibility from the public areas unless specifically approved in writing by the Landlord.
-
The use of corporate crest, logo, or insignia shall be permitted within the area identified.
-
Manufacturers’ labels, underwriter labels, clips, brackets, or any other form of extraneous advertising attachment and/or lighting devices shall be fully concealed from public view.
-
All primary store identity signs shall be required to be dimensional with sculptural objects and fabricated of multiple spaced layers of materials to create a three-dimensional appearance. It is desired that the multiple layers are sufficiently offset to create shadow-lines when exterior illuminated.
-
Letters or text shall be fabricated as dimensional forms, individually cut or formed.
-
Each sign assembly shall provide its own background behind the text which is to provide contrast and ensure legibility. The profile of the background should be creative and distinctive in shape to express the character of the store concept.
-
Acceptable materials include metal, acrylic, wood, glass, or other approved materials when painted or exposed finishes. Plastics must comply with the building code for flame spread and smoke development ratings and construction sustainability requirements.
-
Tenant signs may employ small accent light sources as a design feature or employ concealed supplemental lighting (not backlighting) when approved by the Landlord.
-
Tenants may suggest other types of signs for consideration, but the Landlord must give approval prior to final design and fabrication.
-
The Landlord has final approval on all Tenants’ signage.
-
A creative approach to storefront signage as an integral part of the storefront design is encouraged. Aside from the size and location identified as the “maximum allowable sign area” illustrated in Figures 3.6 and 3.7. Signs that simply fill in the allowable sign area will not be approved.
-
Tenants will be allowed to install one sign at the storefront as a primary business identity; this sign will be limited to trade name and logo only.
-
In the case of a space with two sides of exposure, identification signs are permitted for each frontage.
-
All sign lighting shall be controlled by a time clock with hours of illumination to be determined by the Landlord. MAC reserves the right to suggest operations based on use.
-
The maximum height of the sign letter shall not exceed 14 inches and the maximum height of any individual letter shall not exceed 20 inches.
-
The maximum length of the sign shall not exceed 70% of the total storefront width.
-
Provisions for illumination of primary store identity signage will be supplied by Tenant. Brightness of signs is subject to Landlord approval.
-
Hand leafed/painted silk screened, or decal signing of display windows are permitted. Signs which will display Tenant name and logo only will not exceed 2’ x 2’ square and located a minimum of eight vertical feet from level of the concession’s entry floor.
-
Signs recessed within the storefront lease line may be externally lit from recessed or specifically approved decorative features with all attachments, wiring, clips, transformers, tubes and other mechanisms concealed
-
-
-
Sign Restrictions
-
The following guidelines and restrictions apply to the fabrication and installation of storefront signage and signage within the Tenant’s premises:
-
Tenants are prohibited from affixing permanent or temporary signing, decals, credit card signs or symbols, artwork, or other signage indicating product line.
-
Permanent or temporary interior signage specifying products and prices must be designed, constructed and executed with quality and professional standards of fabrication.
-
Commercially produced graphics for nationally produced and merchandised products are generally unacceptable. Listing of merchandise shall not be permitted within the first five feet measured inward from the lease line.
-
Animated component signs and signs employing moving or flashing lights are not permitted under any circumstances.
-
Surface-mounted box or cabinet-type signs are not permitted.
-
Formed plastic or injection molded signs, or vacuum-formed letter signs are not permitted.
-
Signs fabricated from simulated materials such as wall coverings, stone or wood-grained plastic laminates are not permitted.
- Freestanding floor signs within the first five feet of the store are not permitted.
- Handwritten signs in food service areas will be considered for approval by the Landlord.
- Signs cannot employ exposed raceways, ballast boxes, transformers, crossovers, or conduits.
- Plastics that do not comply with the building and fire codes and construction sustainability requirements are not permitted.
-
-
- Temporary Signs
- Tenants may display holiday decorations within their leased areas. No decorations may be attached from the ceiling.
- Following are pre-approved holidays and event display time frames: Halloween, month of October only; Thanksgiving, month of November only; Christmas/Hanukkah, months of December and January only.
- No illuminated decorations may be used on counter areas. Decorations may sit on the floor or furniture behind counters. Plants or holiday-related decorations may sit on the counters, one per 8’-0” of counter.
- Signs for Concessions in Single Story Common Spaces
- Blade Signs
- Tenant to provide sign permit application at the time of the construction document submission.
- Tenants will be provided a location by the landlord for one two-sided blade sign, typically located on one side of the Tenant storefront.
- All blade signs are internally illuminated. No other lighting is allowed.
- The blade sign aluminum frame, internal light fixtures and associated power shall be furnished and installed by the Tenant.
- The sign face graphics must be consistent with the graphics of the Tenant’s space and may feature a corporate logo as well as the store name. Some locations may require multiple tenants to share a sign.
- Tenant sign panels shall be fabricated from 3/16” #7328 white acrylic sheet stock cut to 15 5/8” x 15 5/8” size with two panels to be provided per sign.
- A background color shall be provided using 3M translucent or opaque film applied to the exterior surface. Use of the white acrylic panel as a background is not permitted.
- Graphics and copy shall be provided using 3M translucent film applied to the exterior surface or the use of exposed white acrylic panel is permitted.
- Tenant shall submit shop drawings and film color representations for sign panels to the Landlord for approval prior to fabrication.
- Blade Signs
- General Guidelines
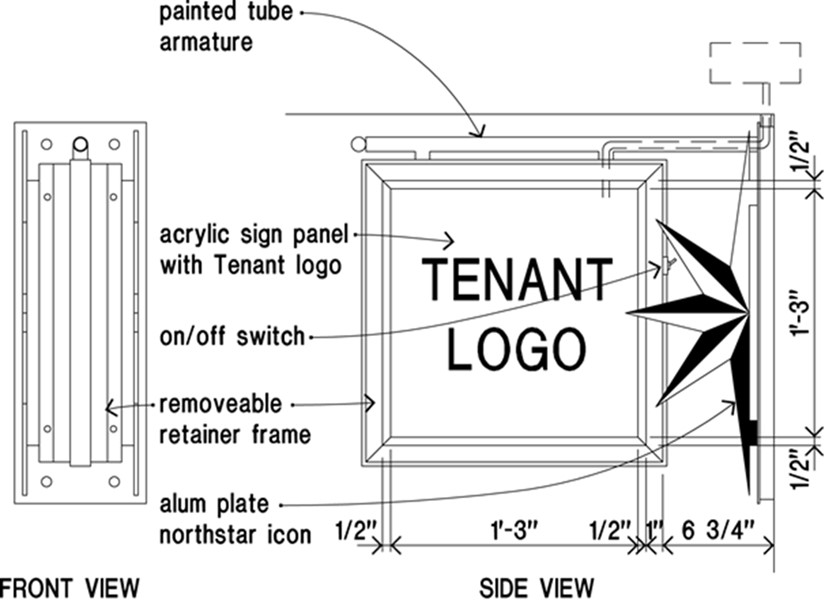
-
-
Storefront Signs
-
Storefront signage complying with Sections 6.1, 6.2, and 6.3 may occur on the sign band provided by the Tenant.
-
The maximum average size of the sign letters is 12” and the maximum height of any individual letter is 14”.
-
-
Signs for Concessions in Multi-Story Spaces
-
Blade signs
-
Retail Tenants are entitled to one two-sided blade sign projecting perpendicular to the storefront. The blade signs will be located on the centerline of a neutral pier as determined by the Landlord.
-
All blade signs are externally illuminated with lighting integral with the blade sign frame. No other lighting is allowed.
-
The blade sign stainless steel frame, light fixtures, power, and sign panel connections shall be furnished and installed by the Landlord. The sign panel and connections to frame shall be designed, furnished, and installed by the Tenant.
-
The sign face graphics must be consistent with the graphics of the Tenant’s space and may feature a corporate logo as well as the store name. Three-dimensional treatment is required.
-
The sign panel may be of any shape,but must not exceed the dimensions shown on the illustrations.
-
The weight of the sign panel must be compatible with the structural design of the blade sign frame. Maximum weight is 75 lbs.
Multi-Story Common Space Blade Sign - Storefront Signs Signage shall comply with the criteria in Sections 6.1 and 6.2 and 6.3.
- The maximum height of the sign letters shall not exceed 14” and the maximum height of any individual letter shall not exceed 20”.
-
-
-
- Mechanical, Electrical, Telecommunications, Fire Protection, Lightning Protection, and Construction Sustainability
- Mechanical Systems Design Criteria
- Objective: The objective of the Mechanical Systems design criteria is to provide the Tenant with specific instructions for meeting the Metropolitan Airports Commission (MAC) basic criteria for construction materials, means and methods. The MAC will require and maintain the same standards for all Tenants. Incomplete drawings, inferior design or poor construction are unacceptable and will not be permitted.
- Licensed Professional Engineer: A professional engineer licensed in the state of Minnesota shall prepare all calculations, drawings and specifications in accordance with the MAC Mechanical Systems Design Criteria, all applicable codes and recognized engineering practices.
- Project Review: The MAC will review drawings for general compliance with the Mechanical Design criteria. It is the Tenant’s responsibility to ensure that the Tenants system will perform satisfactorily and is in compliance with all applicable codes and regulations.
- Submission Requirement: The Tenant shall submit complete plans and specifications to the MAC for Mechanical work consisting of the following:
- HVAC, plumbing, and fire protection floor plans
- Plumbing riser diagram indicating pipe sizes and connection points
- Heating and cooling load calculations
- Supply air, chilled water, hot water requirements[AV4] [AV5] [IR6]
- As-built drawings upon project completion
- General Codes: Comply with the current issues of the MN State Building Code, governing local and state codes and ordinances, and MAC Design and Construction Standards and construction sustainability requirements. The most restrictive will prevail.
- Mechanical Room Access: All work performed by the Tenant’s mechanical contractor within MAC mechanical rooms shall be performed under the supervision of the MAC facilities personnel or their designated representatives.
- Temporary Mechanical: The Tenant shall be responsible for all labor, materials, equipment and related services necessary to furnish, install and connect temporary heat or ventilation.
- General Requirements
- The Tenant shall furnish and install all mechanical work required for and within the Tenant premises.
- Mechanical system modifications requiring shutdown of other portions of the mechanical systems shall be done between the hours of 11 p.m. and 5 a.m. or as coordinated with MAC. Tenant shall notify the Landlord a minimum of two weeks prior to the shutdown requirement and coordinate with MAC and its consultants for issuance of Shutdown Notifications.
- Obtain permission from the MAC prior to core drilling through floors or roof structure.
- Cutting and patching to be performed by Tenant as required shall original finishes to their original condition.
- Floor and wall penetrations must be sealed and dampered, as required per the building code or MAC Standards, to maintain separation requirements.
- Welding or any other hot work requires a hot work permit from MAC and must comply with the MAC Fire Department regulations.
- As-built drawings are to be maintained by the Tenant mechanical contractor and submitted to the MAC. Record exact pipe, duct, and equipment routing and location, and sizes of equipment.
- All penetrations in mechanical rooms are required to have curbing that is fully water proofed. Water proofing is to be compatible to existing water proofing.
- Identification and Labeling is required for all equipment, pipes and ducts within the Tenant space. See MAC Design and Construction Standards, Chapter 15075 for specific requirements. Precede required label characters with the Tenant name and Room Number.
- Plumbing Criteria
- All plumbing plans must be submitted to the MAC Permits Department and will be distributed for review and approval prior to construction.
- Demolish all abandoned conduit, piping, hangers and patch holes through walls and floors.
- Cap all abandoned piping.
- No piping shall be provided over electrical or communications rooms.
- Only clevis and trapeze hangers are allowed.
- All floor piping penetrations shall be provided with a link seal.
- All tenants shall submit a plumbing fixture schedule with fixture connection sizes and fixture unit demands.
- No fiberglass floor sinks are allowed.
- Domestic Water Piping
- Minimum piping size is ¾”
- Provide shutoff valves on piping within the tenant space
- Landlord provides cold water only to the lease line. Tenant is required to provide water heater to meet Health Code requirements.
- No plastic pipe is allowed.
- Gas piping: Provide labels on piping every 5’
- Sanitary and Vent Piping
- Provide a grease trap on all three compartment sinks
- All dishwashers, glasswashers, and food prep sinks must be directly connected.
- Provide telltale drains on all dishwashers, glasswashers and food prep sinks.
- Plastic piping is only allowed within the tenant space, above the floor and below the ceiling, not enclosed in the walls.
- Provide insulation on all p-traps.
- Provide full size cleanouts.
- Provide all floor drains with an approved waterproof membrane.
- Any existing piping to be reused must be augured and pressure tested before being reused.
- Provide cleanouts through the floor in the ceiling space on the level below.
- All piping from bar sinks and soda dispensers to be stainless steel. Drains, traps, and piping back to mains included.
- Beverage lines
- All syrup lines are to be within beverage conduit with long sweep elbows.
- Provide a sink upstream of the beverage station.
- Beer tap drain lines must be installed to flow directly into a floor drain and cannot drain into an under-bar drain table.
- Fire Protection Criteria
- Section 15300 – Fire Protection System of the MAC Design and Construction Standards shall apply to all tenant sprinkler systems.
- Prior to installation, sprinkler shop drawings shall be submitted to the MAC Consulting Engineer and MAC Fire Marshal for review and approval.
- System tie-in and testing shall be coordinated with MAC Fire Marshal and MAC Plumbing Department. System shall not be deemed “acceptable” until approved by the above parties.
- Each new or renovated tenant space shall be a separate sprinkler zone. Tenant is responsible for revising existing sprinkler systems as required to protect tenant space from a single zone. Zone naming shall be as directed by MAC Fire Marshal and MAC Plumbing Department.
- Provide signage and map at control valve assembly to indicate boundary of tenant sprinkler zone.
- Sprinkler system in tenant space must be active prior to occupancy.
- Provide wet chemical hood suppression system in grease hoods. System shall activate by fusible link and manual pull station. Suppression system to be monitored by Fire Alarm system. All appliances shall shut off when system actives. Hood shall remain running upon activation. Appliances can only be turned on when the ventilation hood is operating. Building make up air shall shutdown if there is dedicated make up air at the hood.
- HVAC Criteria
- Verify with MAC Facilities the type of HVAC system required for Tenant’s location (variable air volume, hot/chilled water system, constant volume dual duct, or tenant provided).
- Air quantities may be limited. Submit design requirements to MAC Facilities for review and approval.
- Ductboard is not allowed.
- Ductwork shall be insulated. All insulation shall be external. No internal duct insulation is allowed. See MAC Design and Construction Standards for requirements.
- Piping shall be insulated and provided with identification and directional markers as noted above.
- All plans and specifications to be reviewed by the MAC’s Energy Management Center (EMC) and Mechanical Engineers for approval prior to construction.
- Any tenants who are providing exhaust hoods for equipment are required to provide makeup air in accordance with the MAC DCS. The MAC standard is 100% makeup air provided by a dedicated unit. The unit is to be installed and maintained by the tenant. 90% of the air is to be provided at or near the hood in the kitchen area. 10% of the air is to be provided into the ceiling plenum or tenant seating area. All makeup air units are to provide both heating and cooling for the air. The air is to be tempered to 50 deg F in the winter and 70 deg F in the summer. Make up air is to be interlocked with exhaust fans and any cooking equipment.
- Make sure that OSHA and State Mechanical Code requirements are met for safety regarding all roof mounted equipment. This includes adding railings for fall protection as required by OSHA and MAC. See also Appendix B.
- Any DX condensers for makeup air units or coolers should be either on the roof or be provided with supply and exhaust air to remove the heat from the space.
- All new VAV boxes need to be tied into the MAC’s controls system. All numbering of VAV boxes is to be provided by MAC EMC. Consult the MAC EMC or their consulting engineer for this information.
- Provide one VAV box per thermostat, and position the thermostat in a location to properly serve the space (not by heat producing equipment).
- Upgrade existing VAV box controllers where necessary or obsolete.
- All grease hoods are to have an interlock connection to any cooking equipment below them whether electric or gas to ensure that no cooking occurs without exhaust.
- All hoods are to be equipped with timers to ensure they are turned off at night.
- Dishwasher ductwork and access panels are to be properly pitched.
- Provide upblast grease exhaust fans with grease gutters.
- Provide valves on hydronic piping at the mains to each tenant space.
- Any fire dampers are to be in an accessible location, provided with glass access panels and provide their status on the MAC control system.
- Provide MAC Facilities with commissioning reports for the space.
- Update the MAC IMACS (building automation system) master control screens to match the new layouts of the spaces. This is on the MAC’s controls system. Consult the MAC EMC or their consulting engineer for this information.
- Provide MAC with a maintenance schedule and company for duct cleaning, equipment maintenance, grease trap maintenance, etc.
- Provide reporting in accordance with construction sustainability requirements to MAC Concessions designated personnel.
- Provide a duct pressure test to meet the following requirements:
- Water Test: Type I ducts
- Air Test: Type II ducts
- Demolish all existing unused equipment, piping, ductwork, hangers, wiring and pneumatic tubing.
- Provide accessible labeled locations for all VAV boxes.
- Allow for proper airflow around all existing fin tube radiation if a partition is placed in front of it.
- Provide the proper ventilation to ceiling mounted transformers.
- Ductmate sandwich grease access doors are not allowed.
- Any roof mounted ductwork is only allowed by approval from MAC EMC.
- Electrical Systems Design Criteria
- Objective: The objective of the Electrical Systems design criteria is to provide the Tenant with specific instructions for meeting the Metropolitan Airports Commission (MAC) basic criteria for construction materials, means and methods. The MAC will require and maintain the same standards for all Tenants. Incomplete drawings, inferior design or poor construction are unacceptable and will not be permitted.
- Licensed Professional Engineer: A professional engineer licensed in the state of Minnesota shall prepare all calculations, drawings and specifications in accordance with the MAC Electrical Systems Design Criteria, all applicable codes and recognized engineering practices.
- Project Review: The MAC will review drawings for general compliance with the Electrical Design criteria. It is the Tenants responsibility to ensure that the Tenants system will perform satisfactorily and is in compliance with all applicable codes and regulations.
- Submission Requirement: The Tenant shall submit complete plans and specifications to the MAC for electrical work consisting of the following:
- Electrical floor plans
- Electrical riser diagram indicating sizes and types of feeders, fuses, disconnect switches, main breakers, transformers, etc.
- Panelboard schedules indicating all breaker sizes and loads
- Electrical load summary including connected and demand load calculations
- Light fixture schedule
- Provide as-built drawings upon completion
- General Codes: Comply with the current issues of the National Electrical Code, governing local and state codes and ordinances, and MAC DCS.
- All materials shall be listed or labeled by an independent testing laboratory (UL, CSA, ETL, etc.) where standards or listings exist.
- Electrical Room Access: All work performed by the Tenants electrical contractor within MAC electrical rooms shall be performed under the supervision of the MAC electrical shop or their designated representative.
- Service
- Voltage to each tenant space varies by location:
- 120/208V, three phase, 4 wire with ground
- 277/480V, three phase, 4 wire with ground
- The Tenant shall balance all phases of the Tenant’s electrical system upon completion of construction to within ten percent.
- Each Tenant space shall have a main disconnecting means.
- Voltage to each tenant space varies by location:
- Temporary Electric: The Tenant shall be responsible for all labor, materials, equipment and related services necessary to furnish, install and connect temporary lighting and power.
- General Requirements
- The Tenant shall furnish and install all electrical work required for and within the Tenant premises.
- All necessary permits, inspections and insurance shall be obtained and paid for by the Tenants electrical contractor. State of Minnesota Electrical Permit is required.
- Electrical system modifications requiring shutdown of other portions of the electrical system shall be done between the hours of 11 p.m. and 5 a.m. or as coordinated with MAC. Tenant shall notify the Landlord 21 days prior to the shutdown requirement and coordinate with MAC and its consultants for issuance of Shutdown Notifications.
- Meters should be provided and reporting shall be in accordance with sustainability and billing guidelines. Obtain permission from the MAC prior to core drilling through floors or roof structure.
- Cutting and patching to be performed (as required) by Tenant to return original finishes to their original condition.
- Welding or any other hot work requires a hot work permit from MAC and must comply with the MAC Fire Department regulations.
- No work shall be performed on energized equipment.
- As-built drawings are to be maintained by the Tenant electrical contractor and submitted to the MAC Electrical Department. Record exact conduit routing and location, devices, lights and sizes of equipment.
- Identification and Labeling is required for all equipment, conduit and boxes within the Tenant space. See MAC Design and Construction Standards, Chapter 16040 for specific requirements. Precede required label characters with the Room Number for equipment.
- Raceways and Fittings: In accordance with MAC DCS, all power wiring and systems shall be installed in conduit without exception. Raceways to be rigid or intermediate galvanized conduit or electrical metallic tubing.
- Conductors
- All power conductors to be copper, 600V class, type THWN-2, XHHW-2 or THHN-2.
- Aluminum conductors are prohibited.
- Outlet Boxes: Galvanized steel, 4” square, 25 cubic inch with device plaster/tile ring.
- Wiring Devices
- Receptacles: 20A specification grade, Hubbell 5352 or equal.
- Switches: 20A specification grade, quiet type, Hubbell 1221 or equal.
- GFI Receptacles: 20A, installed where required.
- Motors and Motor Starters
- ¾ HP and above shall be three phase type.
- Manual motor starters with overload protection for fractional horsepower motors. Three phase starters with overloads in each phase for integral hp motors.
- Combination starters to be motor circuit protectors or rejection fuse type.
- Disconnect Switches: NEMA heavy duty, fused or non-fused, horsepower rated.
- Panelboards and Circuit Breakers
- Panelboards to be dead front, 3 phase, 4 wire, constructed with code gauge steel, door in door construction.
- Circuit breakers: bolted line and load terminals, quick make/break. Multipole breakers to have common trips.
- Space for 20% space capacity of 1 pole breakers.
- Grounding: All raceways and outlets, all non-current carrying metal parts, all non-electrical equipment, switching enclosures and electrical protective devices to be solidly grounded in accordance with the National Electrical Code.
- Transformers
- Dry type, 480V Delta-120/208V wye with 220 degree C insulation, 150 degree C maximum temperature rise two winding with voltage adjusting taps.
- Final connections to transformers shall be made with flexible metallic conduit or liquid tight flexible metallic conduit where cleanability is required, such as a food service tenant where transformer is located in kitchen space.
- Minimum length is 12”, maximum length is 60”.
- Transformers located in kitchens need to be proposed to and approved by Hennepin County Environmental Health.
- Lighting Fixtures
- LED Fixtures:
- Shall have a Color Rendering Index (CRI) of 80 or higher.
- Lamp Temperature: 3000k or 3500k
- Power Supplies:
- Minimum efficiency of 85%
- UL Class I or Class II output
- Power Factor (PF) of ≥ 0.90
- Total Harmonic Distortion (THD) of ≤ 20%
- Comply with FCC 47 CFR part 15 non-consumer RFI/EMI standards
- Comply with Reduction of Hazardous Substances (RoHS)
- Exit and Emergency Lights
- Provide per code.
- Exit and Emergency lights must be reviewed and approved by MAC Building Official and MAC Fire Marshal.
- Exit signs shall be LED type:
- Red letters on white face at Terminal 1-
- Green letters on aluminum face at Terminal 2
- LED Fixtures:
- Telephone/Communication Service
- The tenant Electrical Contractor to provide a one inch (1”) conduit from the facility telephone terminal board to a point within the premises for the Tenants telephone service.
- The Tenant is responsible for all conduit, wiring and devices within the Tenant space.
- The Tenant shall be required to furnish and install telephone cabling in conduit from the Tenant premises to the telephone backboard
- The Tenant shall be required to coordinate the connection at the terminal backboard with the owner’s representative and CenturyLink.
- Fire Alarm System
- The MAC requires fire alarm system connections compatible with the owners existing Honeywell XLS 1000. The following are general requirements to be reviewed with, and approved by, the owner during the design phase.
- A fire alarm system connection available at or near the Tenants premises.
- Installed fire alarm detection devices connected to the owner’s system are required to be compatible with the owners fire alarm system and shall be the make and model number specified by the owners representative.
- All conduit, wiring and devices in the Tenant space is the responsibility of the Tenant.
- Connection is required to flow and tamper switches within the Tenant space.
- Tenants’ HVAC system duct detectors (over 2000 cfm) to shut down the system motors and alarm the fire alarm system.
- Smoke detectors are required. They shall be addressable.
- Coordinate device installation work with the MAC’s representative and coordinate all testing and final adjustments.
- Wiring for alarm stations shall be THHN with 6 to 8 twists per foot, #14 or #16 gauge wire twisted pairs installed in conduit. Wiring shall be color coded as per following:
- FS90 bus - yellow/red twisted pair
- Loop 1 - red/black twisted pair
- Loop 2 - orange/black twisted pair
- Loop 3 - blue/black twisted pair
- Loop 4 - yellow/black twisted pair
- Loop 5 - purple/black twisted pair
- Loop 6 - orange/blue with black tracer twisted pair
- Loop 7 - brown/black twisted pair
- Loop 8 - yellow/red with black tracer twisted pair
- Loop 9 - brown/red with black tracer twisted pair
- Loop 10 - blue/yellow with black tracer twisted pair
- Power Supply - (+24 VDC) power - #14 red THHN
- Power Supply - (-24 VDC) common - #14 black THHN
- Door Holders - (+24 VDC) power - #14 blue THHN
- Door Holders - (-24 VDC) common - #14 black THHN
- Modules to Devices - yellow/red twisted pairs in a class “A” four wire loop
- The MAC requires fire alarm system connections compatible with the owners existing Honeywell XLS 1000. The following are general requirements to be reviewed with, and approved by, the owner during the design phase.
- Lightning Protection Systems
- In areas where an existing lightning protection system is installed, any new roof mounted equipment installed by the Tenant shall have protective equipment installed to meet UL96A requirements. Bond to the existing lightning protection system.
- Mechanical Systems Design Criteria
- Construction Sustainability Requirements
- These requirements are intended to help tenants understand and take full advantage of the high-performance features at MSP and provide guidance in ways that tenants can reinforce these features in their own spaces. MAC requires tenants to meet or exceed MAC’s sustainability design and construction goals. MAC has targeted LEED Gold certification unless specified otherwise in the specific tenant request for proposal. The LEED for Interior Design & Construction (LEED ID+C) rating system will be used as a basis for design and reporting. The intent of LEED ID+C is to incorporate tenant spaces into the larger MAC campus. For new buildings tenants also have the opportunity to use LEED for Building Design & Construction (LEED BD+C) if that is a better fit for the project.
- Letter of Intent: Tenant will provide a signed letter of intent prior to construction start to MAC confirming that the construction documents for tenant spaces will be implemented as designed according to the sustainability requirements.
- Initial Reporting: Tenant will submit anticipated LEED Scorecard and any relevant documentation during CPIT review.
- Final Reporting: Tenant will submit scorecard and required documentation for LEED certification to designated MAC personnel at the closeout of the project or as needed by MAC construction team. Tenant is not required to certify spaces with United States Green Building Council. Tenant will be required to coordinate on any follow-up information needed by MAC if MAC decides to pursue LEED certification for the area that houses the concession.
- LEED: the current version of LEED shall be used to determine credits and scorecard points unless otherwise directed. Prerequisites for LEED ID +C and the credits and items listed below are required. Other credits to achieve LEED Gold are at the discretion of the tenant
- Utility Metering: Metering is required for electricity and domestic water. Coordinate with MAC on type and reporting
- Construction Activity Pollution Prevention (LEED BD+C) is required
- LEED ID+C Requirements:
- IP Credit: Integrative Process
- Achieve at least 1 point for this credit
- WE Credit: Indoor water use reduction
- Meet the required prerequisite water reduction of 20%
- Target additional water reduction efforts that align with credit requirements for 40% reduction in indoor water use, 50% is preferred
- EA Credit: Optimized Energy Performance
- Meet the modeling requirements of the prerequisite
- Achieve a 15% reduction in energy usage
- EA Credit: Enhanced Refrigerant Management
- Achieve at least 1 point for this credit
- EA Credit: Enhanced Commissioning
- Achieve at least 5 points for this credit
- MR Credit: Construction and Demolition Waste Management Plan
- Achieve at least 2 points for this credit
- MR Credit: Building Product Disclosure and Optimization - Environmental Product Declarations
- Achieve at least 1 point for this credit
- MR Credit: Building Product Disclosure and Optimization - Sourcing of Raw Materials
- Achieve at least 1 point for this credit
- MR Credit: Building Product Disclosure and Optimization - Material Ingredients
- Achieve at least 1 point for this credit
- IEQ Credit: Enhanced Indoor Air Quality Strategies
- Achieve at least 1 points for this credit
- IEQ Credit: Construction Indoor Air Quality Management Plan Construction Requirements
- IP Credit: Integrative Process
- Tenant Contractor Check-In
- Prior to commencing work in the tenant space, the Tenant’s Contractor shall comply with the following:
- The lease agreement between the Tenant and the Landlord must be fully executed.
- No construction shall begin until written approval of all plans and sign details has been made by the Landlord and such approval is on file with the Landlord. Maintain one (1) set of Landlord approved working drawings and specifications on site during construction.
- Provide evidence of building permits for all trades as required.
- Provide Landlord with certificates of insurance as specified in the lease agreement as well as Payment and Performance Bonds.
- The Tenant’s Contractor must give the Landlord a minimum of five working days’ notice prior to the start of construction.
- Prior to commencing work in the tenant space, the Tenant’s Contractor shall comply with the following:
- Contractors and Subcontractors Insurance
- The Contractor shall not commence work under this contract nor allow any subcontractor to commence work until all insurance hereinafter required has been procured and such insurance approved by the Landlord. Insurance as hereinafter provided shall be kept intact and in force throughout the term of this contract.
- The Contractors shall furnish four (4) copies of an insurance certificate to the Landlord using the standard ACORD form (current date) as evidence of the required insurance. The certificate shall indicate that at least 15 days prior notice will be given to the insureds in the event of cancellation, non-renewal or any material change in the policies. The insurance certificate must be signed and dated by an authorized representative of the insurance company.
- Workers’ Compensation Insurance
- The Contractor shall procure and shall maintain during the life of this contract workers' compensation insurance for all his employees engaged in work on this project as required by statute and shall also require that all subcontractors and sub-subcontractors provide workers' compensation insurance for their employees. Workers' compensation insurance policies shall also provide employer's liability insurance with a limit of $100,000/500,000/100,000.
- Contractors’ Comprehensive General Liability Insurance
- The Contractor shall procure and maintain throughout the term of the contract comprehensive general liability insurance covering personal injury including bodily injury and property damage liability with a combined single limit of $1,000,000 for each occurrence and aggregate.
- The comprehensive general liability insurance shall name the Contractor as insured and shall also name the Landlord as additional insured and shall provide contingent liability for the operations of subcontractors and sub-subcontractors. The insurance shall cover completed operations and products liability as well as broad form contractual liability. The property damage liability portion of the policy shall not contain any exclusions with reference to damage due to blasting, collapse, or underground facilities.
- In lieu of the Landlord being named as an additional insured on the Contractor's comprehensive general liability insurance, the insurance may provide liability coverage for the benefit of the Landlord by means of an Owner's protective liability endorsement or policy.
- Comprehensive Automobile Liability Insurance
- The Contractor shall provide comprehensive automobile liability insurance covering bodily injury and property damage with a combined single limit of $1,000,000 for each occurrence.
- Comprehensive automobile liability insurance shall provide coverage for all automobiles owned by the Contractor and all hired and non-owned vehicles. The Contractor shall also require that all subcontractors and sub- subcontractors maintain the same form of insurance. The Contractor shall also provide contingent automobile liability insurance for the operations of subcontractors and sub-subcontractors to assure coverage as described in this paragraph.
- Builders Risk Insurance
- Unless otherwise provided, the Tenant shall purchase and maintain property insurance upon the entire work at the site to the full insurable value thereof. This insurance shall include the interests of the Landlord as the named insured. This insurance shall provide coverage on an All Risk basis in accordance with the conventional All Risk Builder's Risk forms currently in use. Any loss to the property which would not be covered under the All Risk Builder's risk form which is the result of the carelessness or negligence of the Contractor or Subcontractor shall be borne by the Contractor. Any insured loss is to be adjusted with the Landlord and made payable to the Landlord as trustee for the insured as their interest may appear.
- The policy shall have a maximum deductible of $10,000.00. Each Contractor and Subcontractor shall be responsible for his own coverage up to the deductible amount.
- General Procedures
- The following provisions, with respect to construction procedures, shall be followed by all tenant contractors:
- No equipment, material, or tools will be permitted in the common areas of the Airport.
- No dust will be permitted to be tracked onto the common area floor. The contractor must provide means of cleaning dust from employee’s shoes.
- All equipment, material, tools, or merchandise must be brought through the nearest service entrance. Construction traffic is not permitted in the common areas.
- The passenger elevators and the escalators shall not be used to transport equipment, materials, or tools.
- No material shall be delivered to, or transported through, any public area without the express approval of the Landlord. Any material transported through public areas or stairways, etc., shall be moved on rubber tire trucks, using adequate panels, protective cloths, etc., to safeguard existing floors. Any damage resulting from movement of materials, etc, shall be repaired by the Contractor responsible.
- Confine storage of equipment or material to the demised premises or other locations specifically designated by the Landlord. Stored materials shall not exceed the loading capacity of the floor. Storage in service corridors, truck docks, vacant lease spaces, or other areas is not permitted at any time. Failure to comply will result in removal of all materials with the Tenant bearing responsibility for the costs incurred.
- Smoking is not permitted anywhere in the building, including stores under construction. Smoking areas have been designated by the Landlord.
- The Tenant Contractor shall take all necessary safety precautions to protect workers, the general public, and private and public property and comply with all requirements of the Occupation Safety and Health Act (OSHA).
- The Landlord requires certain work activities to take place between the hours of l0:00 p.m. and 6:00 a.m. as follows:
- Major service disruptions.
- Jackhammering, roto-hammering, core drilling or other noisy operations.
- Work requiring blocking of public entrances.
- All other work which would prevent continuous operation of the building.
- Hauling of demolished material.
- Setting up and removal of construction partitions.
- Delivery of large materials.
- Make arrangements for temporary utility connections as directed by the Landlord and pay the cost of the connections and removal, and all utility charges incurred by the work.
- The following provisions, with respect to construction procedures, shall be followed by all tenant contractors:
- Security of Existing Facilities
- Security of existing facilities must be maintained at all times. When entrance into secure areas is required at any time by workers, it must be coordinated in advance with the Landlord and strict limitations will be set and enforced as to where Contractor personnel can go. Any violations of these limits will subject violator to immediate discharge from this project at the Landlord’s request.
- Airport security
- It is essential that, during the performance of this contract, airport security be maintained and that construction operations within the Air Operations Area conform to the Owner's security requirements.
- Access Gates and Doors. Construction traffic to and from the site and along the designated haul route. The Contractor shall provide a security person whose qualifications have been approved by the Airport Director at the access gate or door at any time the gate is open or unlocked. The security person shall maintain a list of Contractors and Subcontractor personnel who have been assigned to work on this project, and shall permit access only to those persons whose names appear on the list. The Architect, his staff, and MAC staff will also be permitted access upon exhibiting proper identification.
- The Contractor shall provide telephone communications between the security person and the MAC Police Department; the security person shall immediately notify police of any unauthorized access.
- If the access gate or door is found to be open or unlocked and unattended, MAC Police will issue the Contractor a citation under MAC Ordinance No. 41 and the Contractor shall be responsible for all court imposed fines. In addition, a $1,000.00 charge will be levied by the Commission for each violation so documented, and upon final payment the total of any such charges will be deducted from moneys due the Contractor.
- Identification Badges: All contractors and employees will need to be badged by MAC’s badging office. See http://www.mymspconnect.com for current information regarding process, forms, hours, scheduling, fees, etc.
- Construction Vehicles: All Contractor's and Subcontractor's vehicles entering the Air Operations Area must have the company name or logo on the vehicle, prominently displayed for easy recognition. The operation of these vehicles shall be restricted to the construction site and designated haul route. Any delivery vehicles without proper identification shall be met at the access gate and escorted to and from the construction site by an authorized vehicle. In addition, all vehicles operating at the construction site during nighttime hours shall be further identified with flashing amber lights.
- Traffic Control: The Contractor shall provide flagmen as necessary to control construction traffic within the Air Operations Area and as directed by the Landlord.
- Safety During Construction: The Contractor shall inform all construction personnel as to the proper routes, speeds and procedures for transporting equipment and materials to the construction site; and to all restrictions to movement of equipment or personnel within the air operations area. On a daily basis and more often if necessary, all personnel shall be advised of any changes in airport operations that may further restrict his movement.
- Interruptions to Existing Facilities
- All construction activities must be accomplished in such a manner as to permit normal operations within the existing facilities and roadway system to occur at all times. The major areas to be remodeled within the existing facilities will be made available upon written request by the Contractor to the Landlord. Such request shall be made with adequate lead-time so that the Landlord can make necessary adjustments to this operation. These areas must be temporarily enclosed from the remainder of the existing facilities in order that access and all services to the existing facilities can be maintained at all times. The existing interior circulation corridors and required exits must remain open and unencumbered or provisions made for temporary egress.
- All work, including the abandonment or relocation of existing mechanical or electrical utilities, the relocation of existing mechanical or electrical systems or components, or the connection of new mechanical or electrical systems or components to existing facilities, which will cause interruptions to the operations of the existing building and roadway system must be scheduled for times other than normal working hours. The Contractor shall schedule and coordinate his work to minimize the required interruptions, and shall notify the Landlord in writing at least ten (10) working days prior to each intended interruption, indicating the estimated duration of the interruption.
- Keys and Locks
- All keys required by the Contractor during construction require the following deposits:
- $200 deposit for each Schlage key and $500 deposit for each ASSA Cliq key required during the construction period.
- $300 deposit for each construction cipher lock required during the construction period.
- These items can be requested in the MAC Facilities Department with a three (3) business day notice prior to purchase of padlocks.
- All keys required by the Contractor during construction require the following deposits:
- Lockout/Tagout Procedures
- The purpose of the procedure is to establish the minimum requirements for the lockout or tagout of energy isolation devices.
- Contractor shall ensure that procedures are used to ensure that the machine or equipment is isolated from all potentially hazardous energy, and locked out or tagged out before contractor's employees perform any servicing or maintenance activities where the unexpected energization, start-up or release of stored energy could cause injury.
- Examples of stored energy where lockout/tagout applies are:
- Electrical
- Mechanical
- Theremal, Steam
- Chemical, Acids, and Caustics
- Explosives, Natural Gas
- Hydraulic
- Pneumatic
- Gravity
- It is the responsibility of the Contractor to ensure that all appropriate Contractor's employees are instructed in the safety significance of the lockout (or tagout) procedure. Each new or transferred employee and other employees whose work operations are or may be in the area shall be instructed in the purpose and use of the lockout or tagout procedure.
- In preparation for lockout or tagout, the Contractor shall conduct a survey to locate and identify all isolating devices to be certain which switch(es), valve(s), or other energy isolating devices apply to the equipment to be locked or tagged out. More than one energy source (electrical, mechanical, or others) may be involved. Each of these should be listed for each isolation point and a copy forwarded to Landlord. If more than one individual is required to lockout or tagout equipment a multiple lockout or tagout device (hasp) shall be used.
- The basic rules for using the lockout or tagout system are that all equipment shall be locked out or tagged out to protect against accidental or inadvertent operation when such operation could cause injury to personnel. Do not attempt to operate any switch, valve, or other energy-isolating device where it is locked or tagged out.
- A lockout/tagout will be required whenever performing the following work on machines or equipment:
- Required Lockout/Tagout
- Maintenance or service work is defined as constructing, installing, setting up, adjusting, inspecting, modifying and maintaining, and/or servicing machines or equipment.
- Before removal or bypassing any guard or other safety device.
- When an employee is required to place any part of body into a "point of operation" or other danger zone that exits during a machine operation cycle.
- Required Lockout/Tagout
- Exceptions to Lockout/Tagout
- Normal production activities in which lockout cannot feasibly be conducted because of the nature of the operation, provided that the work is performed using alternative measures which provide effective protection.
- Hot tap operations.
- Lockout or Tagout System Procedures:
- Owner Notification: Notify the Landlord that a lockout or tagout system is going to be utilized and the reasons why. Notifications are to be made in the MAC Electrical Department for electrical lockout/tagout, Energy Management Center for mechanical lockout/tagout, and Building Services for plumbing lockout/tagout. Document which of Contractor's employees are to be authorized to perform lockout/tagout, and which areas are affected by the lockout/tagout, and forward a copy to the Construction Coordinator.
- Preparation: Locate all energy sources that need to be isolated.
- Equipment Shutdown: If the equipment is operating, Contractor shall receive prior Landlord approval and shut it down by the normal stopping procedure.
- Affixing Lockout or Tagout: Verify whether there is a specific lockout/tagout procedure developed for the work to be performed, these procedures would be located in MAC Electric Department, Energy Management Center, or Building Services Office. Lockout and/or tagout the energy isolating devices with contractor's individual lock(s) and tag(s). Tagouts are only acceptable in secured equipment rooms requiring special security key for access and the completion of restricted access form or with a person standing by energy isolating device that has been tagged. Lockout will be acceptable in non-secure areas.
- Restoring Locked Equipment to Normal Operation: After the servicing and/or maintenance is complete, check the machines or equipment to ensure that no one is exposed prior to energizing system.
- In the case of a discrepancy between the Contractor's lockout/tagout procedures and the Landlord’s procedures, the Landlord's procedure will prevail. If the Contractor has any questions, they shall refer to the comprehensive MAC Lockout/Tagout Procedure which is located in the MAC Electric Department, Energy Management Center, or Building Services Office. In any event, Contractor shall be responsible for complying with all applicable laws and regulations at all times.
- If the Contractor requires access to a restricted mechanical/electrical room, they shall contact the MAC Electric Department, Energy Management Center, or Building Services Office for the requirement keys and fill out a restricted access form (sample of restricted access form is attached). The Contractor shall contact Operations Department for access after hours. The telephone numbers for the department are as follows:
- Electric Department:612-726-5552
- Energy Management Center: 612-726-5505
- Facilities Department: 612-726-5225
- Operations Department: 612-726-5111
- Contractor represents and warrants that Contractor will comply with all applicable lockout/tagout procedures at all times as set forth in 29 C.F.R., 1910.147 and other applicable laws. Contractor agrees to indemnify MAC and hold MAC harmless from any damages occurring on connection with any failure by Contractor or its agents to observe any applicable lockout/tagout procedures and for any breach of the above warranty, including all damages, costs, expenses, and attorney fees.
- Prior to final payment, all keys, forms, etc. must be returned and signed off by the respective departments. Contractor understands that failure to return any key will require the replacement of all keys and re-keying of all security systems. Contractor agrees to indemnify MAC up to an amount not to exceed $15,000.00 for any replacement and re-keying or other costs MAC deems necessary in its sole discretion upon Contractor's failure to return and obtain sign off for any key.
- Asbestos
- The Landlord has previously engaged an environmental testing company to conduct an asbestos survey for portions of the Terminal 1 Building Complex. Upon written request, the Landlord will make the results of the survey available to the contractor for review. The contractor shall exercise care and diligence in maintaining applicable safety precautions in executing the work in areas containing asbestos.
- Contractors and subcontractors shall comply with all regulations, codes, and laws for the necessary protection of their workers and for the protection of the Landlord, other tenants, and the public when making alternations to work in areas containing asbestos.
- The Landlord has previously engaged an environmental testing company to conduct an asbestos survey for portions of the Terminal 1 Building Complex. Upon written request, the Landlord will make the results of the survey available to the contractor for review. The contractor shall exercise care and diligence in maintaining applicable safety precautions in executing the work in areas containing asbestos.
- Welding and Cutting
- All welding or cutting shall be reported to the MAC Fire Department prior to the start of the job, and upon completion of the project on a daily basis.
- A fire watch shall be provided by the Contractor, suitable fire extinguishers shall be on hand within 20' of the work being performed and accessible at all times.
- Welding or cutting shall cease 1/2 hour before closing the job site for the day and inspected prior to the employees leaving the site for the day.
- Confined Space Entry Regulations
- The contractor shall comply with applicable portions of Federal Regulation 29 CFR S 1910.146 and Minnesota Rules S 5205.1000 and S5207.0300 regarding employee entrance into confined spaces on this project.
- Barricades
- If a construction barricade does not exist in front of the Tenant space, the Tenant will be required to install a dustproof, solid barricade to separate the tenant space from the public occupied common area. All barricades shall extend to the ceiling and be located a maximum of 3 feet in front of the lease line. Construction shall be with metal studs 16” on center and 5/8” gypsum board facing the common areas, taped and painted with primer and two finish coats the color designated by the Landlord. A clear plastic liner shall be installed on the inside to prevent dust migration to the common area. Adequate protection of the mall floor enclosed by the barricade must be provided.
- All barricades shall be without opening or passage to the common area unless the demised premises has no back door. In this case a 3’-0” x 6’-8” hollow core metal door, swinging in, should be installed with a frame, closure device, and lockset. Door shall be painted to match the barricade. The barricade wall or door shall have an identification number showing the previous tenant address number visible to the police.
- Parking
- No parking will be permitted in "NO PARKING" zone and this provision must be strictly adhered to. All construction workers, material suppliers, material handlers, salesmen, product representatives, or other representatives of the contractor are to pay for their own parking on a daily basis in accordance with current posted rates for daily or general parking. Except for the general public, parking will not be permitted in the available short term or hourly lots. No provisions will be made for monthly passes, volume, or discount rates. All unattended delivery vehicles parked at the front entrances to the terminals will be ticketed and towed.
- Trash Removal
- During construction, fixturing, and merchandise stocking of the demised premises, the Tenant shall provide trash removal service at areas designated by the Landlord. The Tenant Contractor shall provide and pay for trash containers and disposal in accordance with sustaianbility requirments. It is the responsibility of the Tenant and the Tenant’s Contractors to break down and remove all trash and debris from the premises on a daily basis and place in the containers supplied for that purpose. No electronics shall be discarded or thrown into the construction dumpsters.
- If the Tenant’s trash is allowed to accumulate for 24 hours or longer within the Tenant’s space or service corridors, the Landlord shall remove the Tenant’s or Tenant Contractor’s trash at a charge of 1.5 times the Landlord’s cost.
- Floor and Roof Penetrations
- Prior to making any roof and/or floor penetrations, the Tenant Contractor must obtain approval of the proposed locations from the Landlord. All cutting, patching, and core-drilling requires written approval by the Landlord before initiating this work. Tenant Contractor is responsible for repairing any damage to reinforcing steel, conduit, wiring, piping, etc., resulting from this operation. The MAC has an outside roofing consultant. Plans must be submitted to them prior to any roofing work being done. Please contact the Permits and Inspection Department for their name and contact information.
- Weatherproofing of all roof penetrations must be performed by the Landlord’s authorized roofing contractor at the Tenant’s expense.
- Floor penetrations in lower level spaces with slab on grade shall be made with a wet saw and replaced with 3,000 psi concrete with 6x6 wire mesh on 95% density compacted fill.
- Floor penetrations in upper level spaces with concrete must be core-drilled. All penetrations must be sleeved and sealed with one pipe permitted per sleeve.
- All upper level floor penetrations shall be completely sealed to prevent permeation of odors or liquids to the space below.